NRE (Non-Recurring Engineering) costs represent the one-time expenses incurred during the design, development, and testing phases of a new product. These costs are distinct from production costs, as they do not directly relate to ongoing manufacturing operations.
When preparing a budget for new product development, accurately assessing NRE costs is crucial for ensuring the project's profitability. Although NRE costs are typically incurred only once, they can be substantial, necessitating that the product has sufficient market potential to generate a return on investment during future large-scale production.
Unlike ongoing production costs, NRE costs are essential upfront investments aimed at successfully launching a new product. In some cases, ODM/OEM manufacturers may enter agreements with specific clients to cover NRE costs, particularly for products that are not manufactured during the development process. Once the product is successfully developed and orders are secured, manufacturers generally reimburse the client for the NRE expenses.
Therefore, in conducting financial analyses, it is imperative to incorporate NRE costs into the budget considerations to ensure that they can be recouped through subsequent production profits, ultimately achieving long-term economic benefits.
NRE Cost Accounting
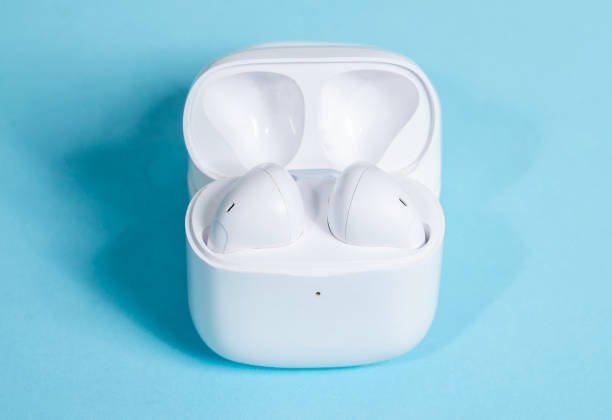
When developing a new product, such as a TWS (True Wireless Stereo) earphone, there are five primary categories of costs associated with NRE (Non-Recurring Engineering):
1. Design and Development Costs
The first category encompasses all expenses related to the design and development of the product. This includes costs for concept development, research, prototyping, and testing.
- Pre-design research
- Industrial design costs for the TWS earphone
- Prototyping expenses
- Sample testing fees
2. Tooling and Equipment Costs
The second category consists of costs associated with the tooling and equipment necessary for manufacturing the product. This includes expenses related to the creation of molds and specialized equipment.
- Mold creation fees
- Equipment depreciation
- Development costs for fixtures
3. Testing and Certification Costs
The third category includes costs related to the testing and certification of the product to ensure compliance with regulations and safety standards. For TWS earphones intended for export to markets like the U.S. or Europe, this involves third-party testing, excluding internal manufacturer testing expenses.
- CE certification fees (for export compliance)
- CCC certification fees (domestic compliance in the manufacturing country)
- Internal testing costs
4. Training and Documentation Costs
The fourth category covers costs associated with developing training materials and documentation necessary for production, assembly, and maintenance.
- Training expenses for assembly personnel prior to production
- Labor and material costs for creating operational procedures, testing protocols, quality control processes, and shipping sampling procedures
5. Marketing and Advertising Costs
The fifth category includes expenses related to promoting the product to potential customers, ensuring adequate market visibility prior to launch.
- Initial brand awareness campaigns
- Advertising expenses
- Endorsement fees
By thoroughly accounting for these NRE costs, companies can better evaluate the financial viability of new product development and ensure they are adequately prepared for the associated investments.
Five Common Reasons for High NRE Costs
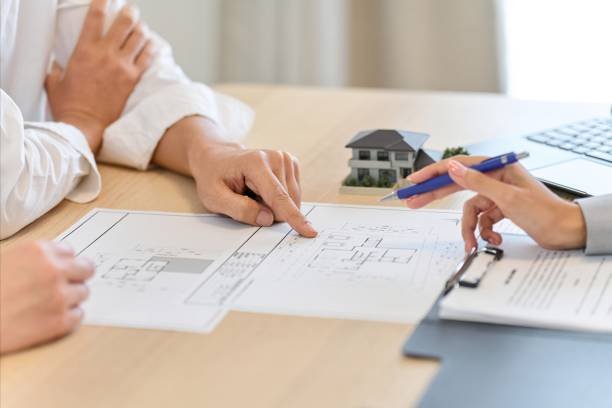
1. Complex Design
One of the primary drivers of elevated NRE costs is the complexity of the product design. Intricate designs necessitate a greater investment of time and resources for development and testing, which ultimately contributes to higher NRE expenses. When a design involves multiple components, advanced technologies, or unique functionalities, the associated engineering challenges can significantly inflate costs.
2. Custom Tools and Equipment
The need for customized tools and equipment is another frequent contributor to high NRE costs. Developing complex products or those with specific requirements often necessitates specialized tooling. For instance, if the battery used in a TWS earphone is not a standard supply chain offering but rather a custom capacity, the costs for both testing devices and the custom batteries themselves can escalate substantially.
3. Regulatory Compliance
Regulatory compliance is a critical aspect of product development, and failure to meet necessary standards can result in severe legal and financial repercussions. However, the testing and certification required to ensure compliance with industry regulations can be both costly and time-consuming. For example, if a TWS earphone sample requires certifications such as 3C or CE, any structural modifications to meet compliance standards can lead to significant increases in NRE costs, potentially doubling them if retooling is necessary.
4. Lack of Experience
A lack of experience within the development team can also lead to inflated NRE costs. Developing new products demands a considerable amount of knowledge and expertise. Inexperienced teams may require additional time and resources to navigate challenges effectively, resulting in increased project duration and costs. Investing in experienced personnel or consultants can mitigate these expenses in the long run.
5. Changes in Requirements
Shifts in product requirements can significantly impact NRE costs. When customer demands or market conditions change, it may necessitate additional design iterations, further development, and extensive testing. These adjustments can lead to delays in product launch and additional costs that were not originally accounted for in the project budget. Establishing clear project scopes and maintaining flexible yet controlled change management processes can help minimize these impacts.
By understanding these common causes of high NRE costs, companies can implement strategies to mitigate risks and optimize their product development processes, ultimately leading to more efficient and cost-effective outcomes.
Strategies to Reduce NRE Costs in Custom Product Development
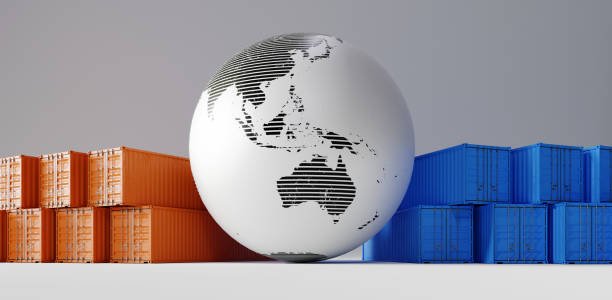
1. Simplify Design
Simplifying the product design is one of the most effective ways to reduce NRE costs. A less complex design generally requires fewer resources and less time for development and testing, which can significantly lower associated expenses. Streamlined designs not only enhance manufacturability but also facilitate quicker prototyping and validation.
2. Standardize Tools and Equipment
Standardizing tools and equipment can lead to substantial cost savings. By utilizing off-the-shelf tools and widely available equipment, companies can reduce the expenses linked to the development of custom tooling. This approach not only cuts costs but also accelerates the production timeline, as standardized solutions are often more readily available.
3. Develop a Regulatory Compliance Plan
Incorporating regulatory compliance considerations from the outset of the product development process can prevent costly modifications later on. By designing products that adhere to relevant industry standards from the beginning, companies can avoid the need for expensive retrofits and ensure that the product meets all necessary certifications without delays.
4. Engage Experienced Manufacturers
Partnering with experienced manufacturers can greatly reduce NRE costs. A knowledgeable team possesses the expertise required to efficiently navigate the product development process, which can lead to fewer mistakes and reduced rework. Experienced manufacturers often have established best practices and insights that can enhance project efficiency.
- Industry veterans with extensive knowledge
- Familiarity with new product development and engineering processes
- Strong communication and project management skills
5. Clearly Define Requirements
Establishing clear and precise requirements at the beginning of the development process helps minimize NRE costs by preventing costly changes during later stages. Well-defined specifications ensure that the final product aligns with customer expectations and complies with regulatory standards, reducing the likelihood of significant redesigns.
6. Utilize Prototyping and Simulation
Implementing prototyping and simulation techniques can identify potential issues early in the development cycle. This proactive approach allows teams to make necessary adjustments before production begins, thus minimizing the costs associated with late-stage changes and ensuring a smoother transition to manufacturing.
7. Leverage Existing Technologies
Making use of existing technologies can diminish the need for custom design and development, thereby lowering NRE costs. Utilizing proven technologies not only streamlines the development process but can also reduce the time and resources required for testing and certification, facilitating a more efficient launch.
8. Collaborate with Suppliers
Engaging in collaboration with suppliers can provide access to their expertise and resources, helping to lower NRE costs. Suppliers may offer cost-effective tooling solutions and assist with testing and certification, leveraging their industry knowledge to benefit the product development process.
Ultimately, each method has its pros and cons, and it is essential to strike a balance between functionality, cost, and time during product development. The primary objective is to meet the needs of the target users while ensuring that the product is both feasible and compliant. By strategically implementing these approaches, companies can effectively manage and reduce NRE costs, leading to more successful product outcomes.
Conclusion
Non-Recurring Engineering (NRE) costs are an unavoidable aspect of new product development. However, by comprehensively understanding the various components that contribute to NRE, the reasons for elevated costs, and the strategies to mitigate these expenses, companies can effectively minimize the impact of NRE costs on their profitability.
Strategies such as simplifying design, standardizing tools and equipment, planning for regulatory compliance, engaging experienced teams, clearly defining requirements, utilizing prototyping and simulation, leveraging existing technologies, and collaborating with suppliers all contribute to reducing NRE expenses.
Ultimately, the key to lowering NRE costs lies in adopting a strategic and proactive approach to product development. By investing time in thorough planning, fostering collaboration among stakeholders, and maximizing available resources, companies can effectively manage NRE costs while enhancing the likelihood of successful product launches. This not only strengthens financial outcomes but also positions the company for long-term success in a competitive market.