Picking and Packing: Core Processes and Best Practices in Distribution Centers
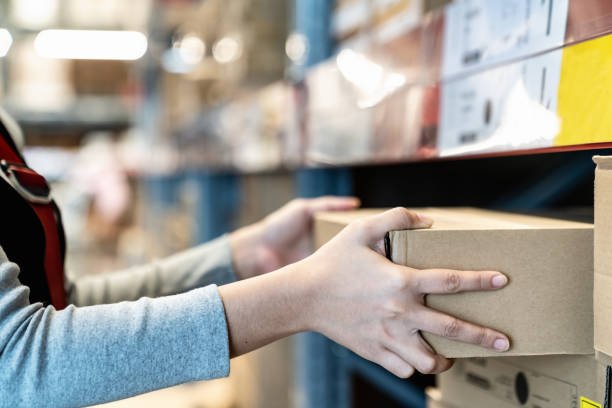
Picking and packing services in distribution centers are key components of modern logistics, involving the selection of products from warehouse inventory and their proper packaging for shipment. This process requires not only high levels of physical labor but also meticulous operation, quick response, and precise execution.
1. The Picking Process
Picking refers to the process of retrieving products from the warehouse based on customer orders. This process typically involves several steps:
- Order Receipt: When a customer places an order, a picking list is generated by the system, indicating the items and quantities to be selected.
- Product Selection: Warehouse workers use handheld devices (such as scanners or smartphones) to locate and retrieve the items from shelves according to the picking list.
- Confirmation and Checking: After picking each item, workers must scan it again to verify its accuracy, preventing errors.
2. The Packing Process
Packing involves consolidating the picked items and placing them into boxes for shipment. This process includes:
- Choosing Packaging Materials: Selecting appropriate boxes, packing materials, and sealing tape based on the type and quantity of items to ensure safety during transport.
- Boxing: Arranging items in the box according to specified order and using packing materials to prevent movement during transit.
- Labeling and Recording: Attaching shipping labels to the outside of the boxes and recording product information for tracking and management purposes.
3. Importance and Challenges
Picking and packing are critical to the operations of distribution centers, directly impacting customer satisfaction and company efficiency. However, these processes come with several challenges:
- High Accuracy Requirements: Picking errors can lead to customer complaints and returns, affecting brand reputation.
- High Work Intensity: Workers must maintain speed and accuracy in a high-demand environment, which can lead to fatigue and mistakes.
- Technological Adaptation: While modern devices can enhance efficiency, some employees may require time to adapt to new technologies.
4. Application of Modern Technology
To address these challenges, many distribution centers are adopting advanced technologies and automation systems, including:
- Warehouse Management Systems (WMS): These systems provide real-time inventory monitoring, optimize picking routes, and enhance efficiency.
- Automated Picking Systems: Utilizing robots and automated equipment to complete some picking tasks, reducing the burden on manual labor.
- Data Analysis and Forecasting: Analyzing historical data to optimize inventory management and picking processes, improving overall operational efficiency.
By implementing these best practices, distribution centers can significantly enhance the efficiency and accuracy of their picking and packing processes, ultimately providing a better service experience for customers.
A Comprehensive Overview of the Picking and Packing Process

To fully understand the concepts of picking and packing, it's essential to grasp the fundamentals of order fulfillment logistics. Once an order is placed, it traverses several stages: receiving goods, inventory storage, picking, packing, shipping, and order processing confirmation.
1. Receiving Goods
The receiving process might seem straightforward, but it is the foundational step in order fulfillment. When products arrive, they must be carefully unpacked and logged into the warehouse system. This applies to both individual manufacturer orders and bulk shipments. After receiving, the items are stored until they are needed for picking and packing. Proper documentation and quality checks during this phase are crucial to ensure that the correct items are received and any discrepancies are addressed promptly.
2. Inventory Storage
While storage may appear to be a minor aspect of the fulfillment process, it is vital for effective inventory management. Accurate tracking of product locations and quantities is essential for smooth operations. This can be achieved through manual methods like Excel spreadsheets, but investing in a robust inventory management system can significantly enhance efficiency and reduce errors. Such systems often provide real-time data, enabling businesses to make informed decisions about stock levels and reorder points.
3. Fulfillment Warehouse
The fulfillment warehouse serves as the hub for picking and packing operations. It should be adequately equipped with sufficient space to store your inventory while ensuring easy access for picking staff. Upon order receipt, employees enter the warehouse, retrieve the required items from shelves, and transport them to the packing station. The organization of the warehouse layout plays a significant role in optimizing picking efficiency, reducing time spent searching for products.
4. The Picking Process
Picking involves selecting the items as per the customer's order. Warehouse staff use handheld devices to scan products, ensuring that they are picking the correct items and quantities. This stage can be enhanced through the use of automated picking systems or robotics, which can speed up the process and minimize human error.
5. The Packing Process
During packing, items are securely placed into shipping boxes or envelopes, ready for transport to the designated warehouse or directly to customers. This step includes:
- Adding Packing Materials: Cushioning materials are often used to protect fragile items and prevent damage during transit.
- Labeling: Accurate labeling is essential, involving the attachment of shipping labels to the package's exterior and internal tags for order identification.
- Bundling Items: Multiple items may be grouped together in a single package, providing a complete order fulfillment.
This packing stage is critical for ensuring that items are well-protected and that all necessary information is conveyed for seamless delivery.
6. Distribution
Once the picking and packing processes are mastered, the products can be efficiently dispatched to customers. Outsourcing fulfillment to third-party logistics (3PL) providers like NextSmartShip can streamline operations. This allows businesses to offload part or all of their logistics tasks, enabling teams to concentrate on other essential areas such as marketing or product development.
7. Order Tracking
After shipment, customers receive an email containing tracking information and additional details about their orders. This seamless process not only enhances customer satisfaction but also provides peace of mind, allowing businesses to allocate more time to other critical activities. The ability to track packages in real-time fosters trust and transparency between the business and its customers.
Exploring Effective Picking and Packing Methods
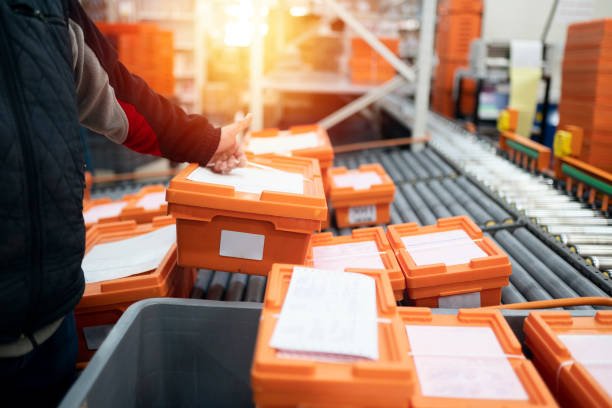
When implemented effectively, picking and packing methods can significantly enhance efficiency, reduce operational costs, and boost productivity. Understanding how each method works and when to apply them is crucial for maximizing flexibility with minimal inventory, resources, and labor while optimizing time management.
1. Item Picking Methods
Single Order Picking
Single order picking involves selecting products for one order at a time, typically conducted within a designated area of the warehouse. This is the most common picking method but is often the least efficient due to the time spent traveling between items, especially in larger warehouses.
Batch Picking
Batch picking consolidates multiple orders into "batches," allowing each picker to handle several orders simultaneously. This method dramatically reduces travel time between picks, as workers can gather items for multiple orders in a single trip. It’s particularly beneficial for high-volume operations, as it streamlines the picking process and enhances throughput.
Zone Picking
Zone picking divides the distribution center into different zones based on product types or SKUs. Orders that contain items from a specific zone are sent to that zone for picking. This method allows for specialization, as pickers focus on particular areas, making the process more efficient. Zone picking can be combined with either single or batch picking, allowing for flexibility based on order complexity.
Wave Picking
Similar to zone picking, wave picking organizes the distribution center into distinct areas but operates on a timed schedule. Orders are "waved" through the warehouse, resembling a snake-like pattern, where pickers gather items for several orders during a single pass. This method requires grouping items based on factors such as size and shape, optimizing travel paths and reducing congestion in high-traffic areas.
2. Packing Strategies
Manual Packing
In manual packing, workers individually pack items into boxes or envelopes. While this method allows for careful inspection of each item, it can be time-consuming, especially during peak seasons. However, it ensures accuracy and allows for customization based on customer preferences.
Automated Packing Systems
Automated packing solutions utilize technology to streamline the packing process. These systems can quickly assemble boxes, fill them with packing materials, and seal them. Automation not only speeds up the process but also minimizes labor costs and human error, making it ideal for high-volume operations.
Batch Packing
Batch packing follows the same logic as batch picking, where items for multiple orders are packed together to increase efficiency. This method can reduce the time spent packing by allowing workers to handle several packages at once, which is particularly useful during busy periods.
3. Key Considerations
When selecting the appropriate picking and packing methods, several factors should be considered:
- Order Volume: High-volume orders may benefit more from batch or wave picking, while single order picking may suffice for smaller operations.
- Warehouse Layout: The physical design of the warehouse can influence which methods are most effective. Zones or dedicated picking paths may enhance efficiency.
- Product Characteristics: Items that vary significantly in size or fragility may require specialized handling, influencing the choice of packing strategies.
The Advantages of Choosing a Picking and Packing Distribution Center
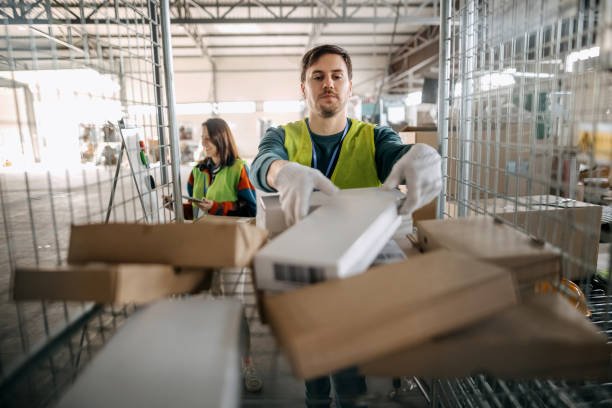
A well-structured picking and packing distribution center can be your secret weapon for business success, especially in the realm of e-commerce. These centers can effectively address one of your most significant challenges: efficient order fulfillment.
In today’s fast-paced market, customers expect their orders to be delivered quickly and on time. However, without the right infrastructure, meeting these expectations becomes nearly impossible. Picking and packing distribution centers provide an ideal solution for businesses of all sizes. If you’re still uncertain about the benefits of utilizing these centers, consider the following reasons to integrate them into your operations.
1. Customization to Fit Your Needs
One of the standout advantages of picking and packing distribution centers is their ability to customize services according to your specific requirements. Whether you need additional storage space, specialized equipment, or extra workforce, many fulfillment centers can adapt to your needs. This flexibility allows you to scale your operations without the hassle of investing in permanent infrastructure.
2. Time Savings
Time is a critical factor in business operations. By outsourcing to a picking and packing center, you can save significant time as they handle the unboxing, sorting, and packing of products for you. This means you can focus on strategic areas of your business, such as marketing, product development, and customer engagement, rather than getting bogged down in logistics.
3. Reduced Administrative Burden
Handling shipping orders comes with a host of administrative tasks, from inventory tracking to printing labels. A picking and packing distribution center takes on these responsibilities, freeing you from tedious management tasks. This reduction in administrative work allows you to allocate resources more effectively, enhancing overall productivity.
4. Decreased Labor Costs
Hiring additional staff can be an expensive endeavor, requiring investment in salaries, benefits, and training. By outsourcing your warehousing needs to a picking and packing company, you can minimize labor costs significantly. You won’t need to worry about recruiting, training, or managing more employees, allowing you to streamline operations and improve your bottom line.
5. Improved Order Accuracy
One of the most significant benefits of using a picking and packing distribution center is the improvement in order accuracy. These third-party logistics (3PL) facilities are dedicated to handling all tasks related to order fulfillment. Their focus on precision ensures that each order is accurately picked, packed, and shipped, leading to higher customer satisfaction and fewer returns.
6. Enhanced Scalability
As your business grows, so do your fulfillment needs. Picking and packing distribution centers can easily scale their operations to match your growth. Whether you experience seasonal spikes in demand or a steady increase in orders, these centers can adjust their services accordingly without requiring you to invest in new facilities or hire additional staff.
7. Access to Advanced Technology
Many modern distribution centers are equipped with the latest technology, including warehouse management systems, automation tools, and inventory tracking software. By partnering with a picking and packing facility, you gain access to these advanced technologies without having to invest in them yourself. This can lead to increased efficiency and better inventory control.
Why Choose ExpNest as Your Picking and Packing Fulfillment Center?

In today’s fast-paced e-commerce landscape, businesses face numerous challenges in order fulfillment. At ExpNest, we simplify the complexities faced by online retailers, providing a streamlined and efficient solution with just a click. Our intelligent inventory system and straightforward picking and packing processes ensure that your orders are processed in the shortest possible time. As an online retailer, you constantly evolve to meet customer demands, and you need a fulfillment center that can keep pace. ExpNest brings the technology, experience, and expertise to help you thrive, supporting businesses as they grow from a single product to thousands, and from local sales to national and international markets.
Advanced Picking and Packing Services
AI-Integrated Robotic Automation At ExpNest, we harness the power of AI-driven Automated Guided Vehicles (AGVs) to enhance your fulfillment processes. These robots utilize sophisticated AI routing technology to automate operations, significantly reducing labor demands and exponentially increasing fulfillment speeds. With productivity boosted by up to 300%, our systems also achieve picking accuracy rates as high as 99.99%, minimizing human error and ensuring precise order fulfillment.
Optimized Fulfillment Processes
When you partner with ExpNest, you can avoid the headaches associated with managing a warehouse. Our state-of-the-art facility is specifically designed to optimize picking and packing workflows. We have developed specialized equipment and processes that ensure the careful handling of your products, resulting in satisfied customers while allowing you to focus on what truly matters—growing your business.
Guaranteed Efficiency
Choosing ExpNest means opting for comprehensive services tailored to support your business. Our warehousing solutions encompass order fulfillment, inventory management, packaging, and shipping. Beyond just picking and packing, we provide end-to-end solutions that cover every aspect of your logistics needs.
Customizable Packaging Options
We understand that every business has unique requirements. That’s why ExpNest offers a variety of customizable packaging solutions. We believe in sustainability and provide eco-friendly packaging options through our PackGreen initiative, along with carbon offset programs that fund reforestation and conservation efforts. This not only contributes to a carbon-neutral future but also helps reduce costs for our clients.
Real-Time Online Tracking
In today’s e-commerce environment, customers expect transparency regarding their orders. With ExpNest, you can provide your customers with real-time tracking information, enhancing their shopping experience and fostering trust in your brand. Our systems ensure that you and your customers are always informed about the status of their orders.
Flexibility to Scale
Flexibility is crucial in fulfillment services. At ExpNest, we offer the adaptability you need to grow your business. Whether you’re starting small or planning to expand, we can adjust our services to meet your evolving requirements. This scalability allows you to respond to market changes without the constraints of fixed resources.
Quick and User-Friendly Solutions
ExpNest is designed for ease of use. Our proprietary software automates many steps in the fulfillment process, from receiving goods and managing inventory to order processing, packaging, and shipping. It’s easy to install and learn, allowing you to spend less time on logistics and more time on sales and customer relationships.
Competitive Pricing
When you choose ExpNest as your picking and packing fulfillment center for shipping from China, you receive world-class services at some of the most competitive rates in the industry. Our fee is just $0.99 per order, which includes picking, packing, and standard packaging materials. This rate is lower than most other fulfillment companies, making it an excellent value for businesses looking to save on logistics costs while still providing top-notch service to their customers.
Conclusion
Incorporating ExpNest into your fulfillment strategy can provide significant advantages. From advanced automation and customizable solutions to real-time tracking and competitive pricing, we offer everything you need to enhance your order fulfillment processes. With ExpNest, you can focus on scaling your business while we handle the logistics. Join us and experience the difference that a dedicated fulfillment partner can make in your operations.